Mit dem Zwilling schneller ans Ziel
IHK-Anwender-Club „Digitale Produktion“: Prozesse in der Produktion simulieren und beschleunigen.
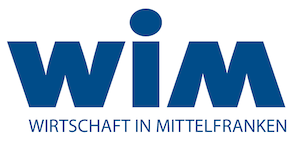
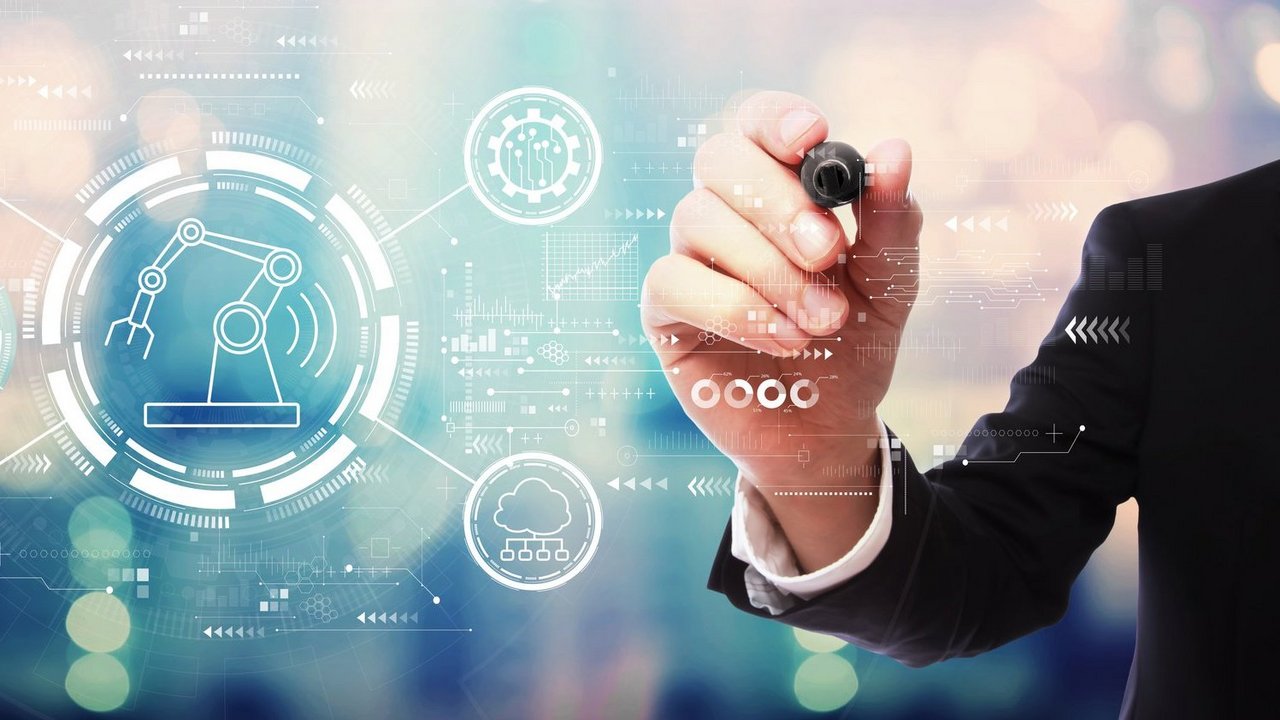
Die Digitalisierung bringt ganz neue Möglichkeiten, um Prozesse in der Industrie effizienter zu gestalten. Der IHK-Anwender-Club „Digitale Produktion“ zeigte auf, wie sich mit digitalen Modellen und Simulationen die Wettbewerbsfähigkeit steigern lässt. Experten erläuterten mit Beispielen aus der Praxis, welche Chancen das sogenannte Digitale Engineering gerade in der Automobilproduktion eröffnet.
Ein zentraler Baustein kann ein digitaler Zwilling sein, der quasi als virtuelles Spiegelbild von Maschinen, Fertigungsstraßen, Konstruktionsplänen oder ganzen Organisationen dient. So lassen sich Prozesse simulieren und optimieren oder neue Produktdesigns im virtuellen Raum ausprobieren. „Ein digitaler Zwilling kann im Betrieb bereichsübergreifend oder auch unternehmensübergreifend genutzt werden“, sagte Oliver Fuhrmann, der bei der IHK Nürnberg für Mittelfranken das Projekt „transform_EMN“ koordiniert (siehe Meldungen Seite 36).
Das Coburger Softwarehaus Schwindt Digital GmbH unterstützt Zulieferer der Automobil- und Luftfahrtindustrie sowie Architekturbüros mit der Plattform „3DExperience“. Sie erlaubt es, virtuelle Zwillinge zu erstellen. Die Möglichkeiten sind vielfältig, führte Digitalisierungsexperte Johannes Morgenroth aus. Es können Produkt-Zwillinge von Maschinen, Fahrzeugen oder Gebäuden sein. Oder Prozess-Zwillinge bilden Produktions- oder Logistikprozesse ab. Mit System-Zwillingen lassen sich z. B. Energieversorgungs- oder Verkehrssysteme virtualisieren.
Morgenroth illustriert das praxisnah mit einem Beispiel aus einem virtuellen Zulieferprozess eines Herstellers von Autositzen. Eine Armlehne wird in 3D-Ansicht konstruiert und im virtuellen Modell angepasst. Dafür können die Entwickler auch unternehmensübergreifend auf die gesamten Unterlagen zugreifen, damit es am Ende passend ist. Im digitalen Zwilling lassen sich auch die Stanzteile bearbeiten, die beteiligten Zulieferer einbinden und der spätere Montageprozess überprüfen. „Referenzkunden können 20 bis 30 Prozent schneller reagieren und liefern“, fasst Morgenroth seine Erfahrungen mit virtuellen Tests und Simulationen zusammen. Zudem würden Produktfehler bereits in der Planungsphase vermieden.
Virtuell planen und in Betrieb nehmen
Die Erlanger Heitec AG präsentierte die Vielfalt der Möglichkeiten, die mit durchgängigen digitalen Lösungen vom Engineering über den Vertrieb bis zum Betrieb von Anlagen möglich sind. Herzstück ist das „HeiVM-Ökosystem“ (Heitec Virtual Machine). Auf Basis einer durchgängigen Digitalisierung können insbesondere Produktionsanlagen virtuell in Betrieb genommen werden. Dafür verfügt der digitale Zwilling über verschiedene Simulationstools und Bibliotheken. Enthalten sind die virtuellen Komponenten etwa von Robotern, Förderbändern und Sensoren, sagte Michael Schnabel, Experte für digitales Engineering bei Heitec.
Mit dem Produktkonfigurator können Vertriebler bereits in einer frühen Entwicklungsphase per Tablet in einer Fertigungshalle des Kunden Varianten und Standorte virtuell vorstellen und Wünsche aufnehmen. Schnabel verweist auch auf eine Konzeptstudie für einen Kunden, um bereits in einer frühen Planungsphase für eine Intralogistik-Lösung die Entscheidung für einen Anbieter objektiv zu bewerten. Dafür simulierte Heitec Abläufe und Materialbewegungen. Der Kunde könne damit Risiken verringern, weil Probleme schon frühzeitig erkannt würden, so Schnabel. Dieses Heitec-Prinzip lässt sich auch für die Planung im Maschinenbau anwenden. Für eine roboterbasierte automatisierte Belade-Einrichtung wurden verschiedene Robotertypen entsprechend den Anforderungen virtuell simuliert.
Schnabel beschäftigt sich auch intensiv mit digitalen Schatten. Hierfür werden zum Beispiel mit Sensoren kontinuierlich Daten von realen Maschinen und Anlagen erfasst, um digitale Zwillinge zu optimieren. Außerdem forscht Heitec an Large-Language-Models (LLM), um in Zukunft komplexe Engineering-Modelle zu standardisieren und deren Entwicklung zu beschleunigen. Dafür sollen etwa auch textbasierte Besprechungsprotokolle in den Prozess mit einfließen.
Technische Dokumentation wird „intelligent“
Für Edgar Hellfritsch, CEO der Fürther doctima GmbH ist klar, dass sich auch die technische Kommunikation beispielsweise von Betriebsanleitungen und Handbüchern verändern müsse. Bei dieser „Wirtschaftslinguistik“ gehe es darum, wie Unternehmen sprechen und schreiben und wie sich korrekte und verständliche Texte formulieren lassen. Hellfritsch illustriert die Diskrepanz an einer persönlichen Erfahrung: Er konnte bei seinem neuen Wagen den Kofferraum nicht öffnen, die 700-seitige Betriebsanleitung des Autos half dabei aber nicht weiter. Das ließe sich mit einem sogenannten „Component Content Management System“ (CCMS) ändern, mit dem man Inhalte in der technischen Redaktion beliebig und modular rekombinieren kann: „Damit wird ein Handbuch genauso individuell wie die Fahrzeugproduktion.“ Dafür wären die Betriebs- und Stammdaten eines digitalen Zwillings mit Anweisungen und Erläuterungen zu verknüpfen. Mit dieser „intelligenten Information“ ließen sich auf einen Schlag etwa in einer App die gesuchten Funktionen finden, beispielsweise wie sich der Kofferraum öffnen und die Klimaanlage starten lässt. „Intelligente Information liefert interaktiv genau die benötigte Information für mein Fahrzeug und zwar jetzt.“ Bei diesen Lösungen sei Deutschland sogar Technologieführer.
Autor: Thomas Tjiang
Webcode: N1123